Verbeteren in coronatijd… Resultaten delen in coronatijd… Een symposium over verbeteren in coronatijd… Het kan en het bleek nog leuk te zijn ook tijdens het symposium Continu Verbeteren van Avans Hogeschool op 26 januari jl. Met een discussie over het thema ‘Intercultureel verbeteren op de werkvloer’ en vijf studenten die hun projecten presenteerden en daarmee kans maakten op het winnen van de ‘best practice award’.
Door Ton van Kollenburg
Jaarlijks wordt de minor Continu Verbeteren afgesloten met een symposium. Dit jaar vond dat wederom online in een kleine setting plaats. Dat betekende dat van de twintig verbetergroepen er vijf werden uitgekozen, waarvan een student het resultaat mocht presenteren. Die presentaties werden voorafgegaan door een tafelgesprek, onder leiding van voormalig NOS-verslaggever Theo Verbruggen, met als gesprekpartners René Aernoudts, directeur Lean Management Instituut, Grit Knopf, directeur Sales & Programs van Maruna, Myke Groeneboer, coördinator van de minor Continu Verbeteren en Ton van Kollenburg, lector Improving Business van Avans Hogeschool.
Thema van het tafelgesprek was ‘Intercultureel verbeteren op de werkvloer’ en Ton trapte af met een kort betoog waarin hij schetste hoe een eindige aarde, een digitale transitie, een vergrijzende arbeidsmarkt en toenemende internationalisering zorgen voor steeds meer nabijheid van culturen – ook binnen bedrijven. Mensen met een verschillende culturele achtergrond moeten samen op de werkvloer aan de slag met het verbeteren van processen, om te zorgen dat hun organisaties zich kunnen aanpassen aan al die veranderingen. Dat leidt op intercultureel gebied wellicht tot mogelijkheden en uitdagingen. Grit Knopf vult aan dat intercultureel verbeteren op de werkvloer ook betekent, dat je in gesprek moet met bijvoorbeeld de directie over wat anders en beter kan: ‘Voor andere culturen is dat geen gegeven. Ik ben zelf Duitse en in het verleden ging ik niet zomaar naar een directeur om te zeggen hoe het anders kan. Zo is in de Duitse cultuur hiërarchie belangrijker, in Nederland is een besluit meer een aanleiding om te gaan discussiëren met elkaar. Een ander aspect is het direct benoemen van problemen, terwijl je in Duitsland andere wegen zult moeten vinden om te horen wat de werkvloer echt vindt, omdat ze niet zo direct zullen zeggen wat niet goed is.’
René Aernoudts vult hierop aan: ‘Wat betreft intercultureel verbeteren op de werkvloer lopen we er nu al tegenaan, dat een groot deel van het werk op de productievloer wordt gedaan door niet-van-origine-Nederlanders. Je hebt dan mogelijk te maken met uitzendkrachten die zeggen dat ze je begrijpen, ook als dit misschien niet zo is. Als wij Nederlanders vragen: ‘Begrijp je het?’ dan verwachten we ook een directe reactie, maar ze gaan ja zeggen, omdat ze bang zijn dat ze anders hun baan kwijt zijn. Dus je moet daar anders mee omgaan. We hebben nu bij een bedrijf een groep Syriërs met een meer traditionele man-vrouwverhouding dan wij gewend zijn. Die accepteren minder makkelijk dat een vrouw ze als teamleider aanstuurt. Voor ons is belangrijk dat we niet in de val trappen dat we onze cultuur daarop drukken, maar dat we ons bewust zijn van ons eigen gedrag als je met die culturen te maken krijgt.’
Uitdagingen en kansen
Intercultureel samenwerken is niet altijd makkelijk met verschillen in taal en elkaar echt proberen te begrijpen als grote uitdagingen. Niettemin zijn er ook kansen. Zo stelt Grit dat Nederland een meer individualistische cultuur heeft en anderen wat collectivisme meebrengen. Dat kan leiden tot een beter samenwerken in teamverband. Ton vult aan, dat andere culturen ook andere inzichten met zich meebrengen en daardoor de creativiteit kunnen verbeteren. Myke vertelt dat ook kleine dingen belangrijk zijn: ‘Bij een van mijn eerdere werkgevers zijn er verschillende diners georganiseerd, van verschillende landen, zodat ieder van zijn of haar cultuur die middag mocht koken en die kreeg ook vrij daarvoor. Dat gaf veel aanknopingspunten naar elkaar om die communicatie te starten en als je dan daarna met elkaar mag gaan verbeteren dan helpt dat ook!’ René sluit af met de stelling: ‘We zouden minder problemen in de wereld hebben als we allemaal meer internationaal zouden kunnen werken, zodat je veel meer ervaring opdoet en begint te snappen: hoe werkt dat nou eigenlijk hier.’
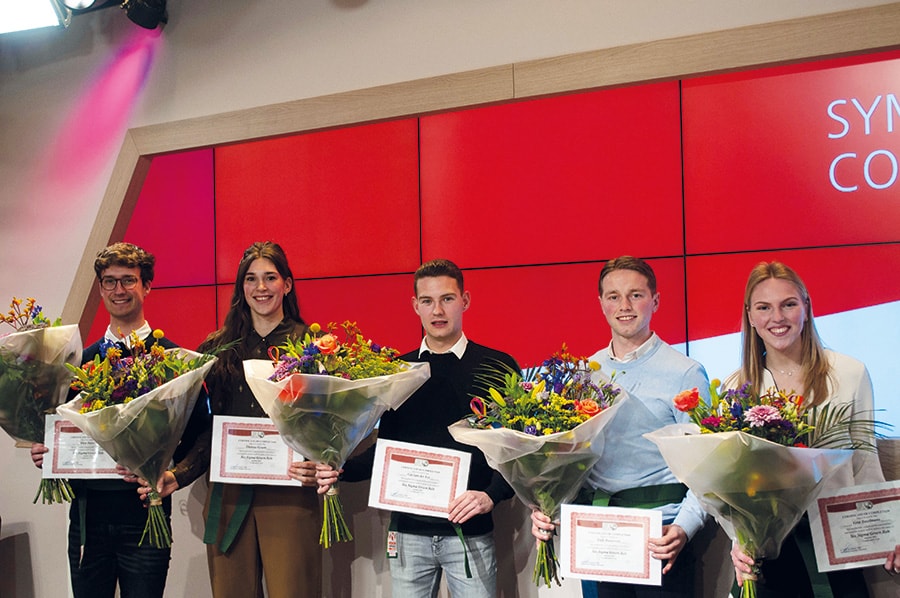
De studenten die hun Six Sigma Green Belt kregen uitgereikt (vlnr): Stan Janse, Shenna Geurts, Cas van der Lee, Niels Banierink en Vera Bazelmans.
Best practice award
Vijf studenten streden tijdens het symposium om de ‘best practice award’. Dat deden ze aan de hand van de verbeterprojecten die ze uitvoerden bij Prodrive, Smink, Bosch, Heijmans en DSV. Natuurlijk keken de gesprekpartners kritisch mee…
Beter gebruik data
Als eerste mocht Vera Bazelmans haar ervaringen delen bij het verbeteren van het ontsluiten van de testgegevens bij Prodrive, producent van onder andere elektrische kabels. Ze vertelde dat tijdens dit testproces data van de gemeten resultaten worden verzameld. Deze data worden opgeslagen in de database, maar daar werd alleen iets mee gedaan als er problemen zijn bij een klant. Die testgegevens kun je natuurlijk ook gebruiken om de prestaties van je producten te volgen. Vera vertelt dat ze allereerst met een meetsysteemanalyse bekeken wat er beschikbaar was aan data en hoe betrouwbaar en volledig die waren. ‘We zagen wel verbetermogelijkheden in de werkinstructie van de meetmethode, maar de betrouwbaarheid en volledigheid van de data bleken dik in orde te zijn, zodat we aan de slag konden met het ontwerpen van een datatool. Daaruit kwamen bij bepaalde productgroepen bijvoorbeeld trends over tijd naar voren, zodat tijdig kan worden ingegrepen en eerder kan worden onderzocht wat de oorzaak is, door bijvoorbeeld apparatuur aan te pakken en te voorkomen dat die trend doorzet en het product buiten de grenzen gaat presteren.’
Verder vertelt ze: ‘Ook hebben we gekeken hoe vaak fails voorkwamen en bij welke productgroepen dit was. Zo kan je bijvoorbeeld achterhalen of je bij dit product nog verder onderzoek moet doen, want fails resulteren natuurlijk in herstelwerkzaamheden voor je medewerkers en dit kost tijd en geld.’ Na ontwikkeling van de datatool, is deze met de stakeholders besproken en verder vervolmaakt. René vindt het in dit project sterk dat ze eerst kritisch naar de dataset hebben gekeken, omdat je anders tot hele verkeerde uitkomsten kunt komen en verkeerde adviezen kunt geven. Hij stelt: ‘Daar zie ik het nogal eens mis gaan.’ Grit bewondert de daadkracht van de studenten: ‘Jullie krijgen DMAIC, jullie krijgen even vijf weken, terwijl de meeste green belts toch wel zes maanden onderweg zijn!’
Problemen prioriteren
Als tweede was het de beurt aan Cas van der Lee om te vertellen hoe hij en zijn medestudenten bij Smink Groep, die cleanroomsamenstellingen ontwikkelt en bouwt, werkten aan een roadmap om problemen met hun bijbehorende prioriteiten zichtbaar te maken. Cas: ‘Elke keer als een productieorder wordt opgestart kunnen verschillende problemen ontstaan. Bijvoorbeeld het ontbreken van materialen bij de start van de productie van die order. Of het ontbreken van documentatie, zoals een tekening. In de huidige situatie worden die problemen wel geregistreerd, maar worden ze niet verholpen of opgepakt.’ Ze startten met het in kaart brengen van het proces, dat complex bleek, doordat er veel afdelingen bij betrokken zijn. Het probleem komt eruit in productie, maar kan zijn ontstaan bij werkvoorbereiding, engineering of kwaliteit. Vervolgens gingen ze aan de slag met het achterhalen van de root causes en het toetsen hiervan aan de hand van historische data. De uitkomsten hiervan verwerkten ze in de roadmap, die het voor Smink duidelijk maakt wat de prioriteit van de problemen is en een tijdspad schetst voor het oplossen ervan. Cas concludeerde: ‘Uiteindelijk hebben we deze roadmap aan onze stakeholders gepresenteerd die erover tevreden waren en de roadmap nu uitrollen.’
René vindt het knap als je zo kunt door vragen. Hij zegt: ‘Ik doe zelf liever 5x waardoor, want waarom trekt soms te veel in het persoonlijke en dan voel ik me aangevallen. Ik kan bijvoorbeeld tegenover je gaan staan, terwijl beter is dat ik fysiek naast je ga staan en we samen kijken naar de oorzaak van het probleem. Dus ik kijk met je in plaats van tegenover je. Tegelijkertijd blijkt dat meer dan 90% van de bronoorzaken niet de bronoorzaak is als je een keer waarom of waardoor vraagt, dus je moet er echt mee aan de slag. En dat vraagt om volharding, dus complimenten aan de studenten!’
Grit was nog wel benieuwd naar de grondoorzaken. Cas gaf aan, dat een daarvan was het ontbreken van een standaardprocedure bij het doorvoeren van een procesverandering. ‘Dat heeft als gevolg dat als een product moet worden gemaakt dat al twee jaar niet meer wordt gemaakt, de procesverandering daar nooit is doorgevoerd, zodat je dezelfde fouten tegenkomt. Hier zijn intussen afspraken over gemaakt.’
Balanceren van de workload
Bij Bosch gingen Niels Banierink en zijn groep aan de slag om te onderzoeken of balanceren van de workload bij de kwaliteitscontrole mogelijk was. Ze letten erop of er sprake is van overeenstemming tussen de theorie en de werkelijkheid. Niels: ‘We hebben eerst gekeken naar de tijden die we op de vloer zagen: met een stopwatch hebben we minstens 25 handelingen gemeten. Bepaalde verstoringen in onze metingen hebben we eruit gefilterd om alleen nog maar met de betrouwbare metingen verder te gaan. Daarvan was bijvoorbeeld sprake als de medewerkers moesten omlopen vanwege de reparatie van een machine.
Vervolgens hebben we gekeken of de tijden die nu in de planning worden gebruikt, vallen binnen de betrouwbaarheid van onze metingen. Valt het daarbuiten, dan gaan we kijken naar de oorzaak: waarom is die afwijking er? Valt het erbinnen, dan kunnen we zeggen: ‘de tijd die gebruikt wordt komt al overeen met de werkelijkheid.’ Op hoofdlijnen bleken de verschillen klein te zijn, maar per activiteit waren wel verschillen zichtbaar, vooral in de aan- en afvoer van het proces. Bij de aanvoer heeft dat te maken met het gebruiken van een andere methode op de werkvloer dan die bij de planning werd gebruikt. Bij de afvoer bleek dat de planning gebruik maakte van één type product, terwijl in werkelijkheid met twee typen product wordt gewerkt, die ook een andere methode vergen. Deze zaken worden aangepast in het planningssysteem en daarnaast wordt het werk wat anders verdeeld over de medewerkers. Niels vertelde dat ze nog een andere verbetermogelijkheid zagen tijdens hun analyse: ‘We zagen dat het personeelsnummer door medewerkers zowel handmatig als digitaal, in de computer, wordt gedaan. Daarvan kan er eentje worden geëlimineerd.’
Ton spreekt zijn waardering uit over de grondige analyse die de studenten hebben uitgevoerd: ‘Zoveel metingen doen als basis om te kijken of de plantijden kloppen, dat is, zeker gezien de beperkte tijd die ze hadden, heel goed.’ Grit vindt het mooi dat de leverbetrouwbaarheid, een heel belangrijke KPI, centraal stond. Het is niet erg dat het niet gaat om hoeveel geld wordt bespaard: hier kan de klant betrouwbaarder worden beleverd.
Sneller weten wat de kwaliteit is
Stan Janse en zijn groep gingen aan de slag bij bouwbedrijf Heijmans dat jaarlijks onder andere ruim een miljoen ton asfalt legt. Dat moet natuurlijk goed en daarom wordt de kwaliteit ervan vastgesteld met een boorkernonderzoek. Nadeel van deze methode is echter, dat het vijf tot tien dagen duurt voordat de resultaten bekend zijn. Daarom hanteert Heijmans al inline-metingen tijdens het storten en walsen van het asfalt. Heijmans wil deze metingen graag gebruiken om de kwaliteit van het asfalt te voorspellen. Uit een eerste analyse – ook met gegevens van het KNMI – bleek een enorme variatie in de data. Met een dataset van 92.000 regels is deze variatie onder de loep genomen en lukte het te komen tot een set van 147 meetpunten. Maar volgens Stan zijn ze nog verder gegaan: ‘Daarnaast hebben we gekeken naar de plaats waar het meetsysteem zich bevindt. Dat bevindt zich achter op de asfaltspreidmachine. Hier recht onder wordt asfalt van 150 graden gestort. Onze hypothese is, dat de warmte van het asfalt de metingen beïnvloedt. Om deze hypothese te testen hebben we vijf scenario’s opgesteld, samen met experts. In een pilot zal een meetsysteem op verschillende locaties bevestigd worden en daarna wordt het meetsysteem dat de meest betrouwbare waardes levert, ingevoerd.’
René vindt dat data enorm helpen om inzicht te krijgen: ‘We noemen dat ook wel point of cause; ofwel waar liggen de oorzaken? Wat hier heel mooi naar voren komt, is het punt waar gemeten wordt, wat wel eens heel belangrijk zou kunnen zijn voor de resultaten. Als het daar 150 graden is dan kan dat best invloed hebben.’ Grit is onder de indruk van de hoeveelheid werk in vijf weken: ‘Jullie hebben een dataset gekregen, daarna nog een andere dataset genomen, daar moet meer dan veertig uur per week in zitten.’ Myke vindt het mooi, dat de studenten zo’n verandering teweegbrengen en daar mensen weer mee vooruit helpen.
Slimmer opslaan
Bij logistieke dienstverlener DSV gingen Shenna Geurts en haar collega’s aan de slag om te zorgen dat DSV beter zou kunnen omgaan met de piekbelasting door een van de klanten en dat de bijbehorende ruimtetekorten zouden worden opgelost. Uit de analyse bleek dat de cratek-boxen, waar die klant veel gebruik van maakte, weliswaar met twee stuks naast elkaar op een ligger konden worden geplaatst, maar dat dat leidde tot 43,5 centimeter aan ruimteverlies. Shenna: ‘Bij een piekperiode betekent dit een ruimteverlies van 75 secties. We waren begonnen met twaalf verschillende ideeën, dus we hebben tot op het niveau van de ‘stock-keeping units’ uitgezocht hoe je dat in een systeem kunt realiseren. We dachten bijvoorbeeld over hele lange doorrolstellingen, maar dat was niet haalbaar, omdat je met zo veel verschillende producten te maken hebt. We kwamen tot een heel compact systeem, waarmee je de opslagcapaciteit per vierkante meter het meest vergroot. Dat werkten we uit in drie mogelijke oplossingen, waarin combinaties van shuttlesysteem, blockstack en pushback werden uitgewerkt. Uiteindelijk bleek voor deze specifieke klant een combinatie van een shuttlesysteem met blockstack de beste oplossing om de opslagcapaciteit van de verschillende pallettypes (Euro, Blok en Cratek) te vergroten.
Ton vindt dat deze groep, net als de andere, mooi gestructureerd aan het werk is geweest en er voor gezorgd heeft om niet in bekende valkuilen, zoals ‘jumping to conclusions’ te stappen. Grit vindt het mooi hoe continu verbeteren, Lean, DMAIC en bedrijfskunde in dit project samenkomen en dat het ook is gelukt om de uitkomsten echt uit te werken in concrete tekeningen en een businesscase. Voor een student ‘Food en Business’ zoals Shenna, was dat bijzonder om te horen: ‘Het bijzondere in deze minor is: Je komt van allerlei verschillende studierichtingen – de twee anderen komen van technische bedrijfskunde en werktuigbouwkunde – en we kenden elkaar niet, maar we hadden wel een leuke groep waarmee we tot mooie oplossingen konden komen en we hebben een leuk project gehad.’
En de winnaar is…
Terwijl de aanwezige studenten hun Six Sigma Green Belt kregen uitgereikt, mochten de online deelnemers aan het symposium stemmen wie de beste presentatie had gegeven. De winnaar bleek Shenna Geurts met haar presentatie over DSV. Wellicht had het enthousiaste teamwork hierin een belangrijke invloed, want na afloop van het symposium belde hun bedrijfsbegeleider, Sander van Gelderen, op om te vertellen dat dit de beste en leukste groep was die hij, in de jaren waarin hij betrokken is bij de minor, heeft gehad.
Foto boven artikel: De presentaties werden voorafgegaan door een tafelgesprek, onder leiding van voormalig NOS-verslaggever Theo Verbruggen, met als gesprekpartners René Aernoudts, directeur Lean Management Instituut, Grit Knopf, directeur Sales & Programs van Maruna, Myke Groeneboer, coördinator van de minor Continu Verbeteren en Ton van Kollenburg, lector Improving Business van Avans Hogeschool.